PRODUCTION RELOCATION
The high complexity of such a project makes it advisable to seek the support of experienced experts in the field. The risks that may arise for your own company should be minimized from the very beginning.
- The relocation of a production line confronts the management with entirely new challenges, especially concerning interface management.
- Multidimensional dependencies characterize each project: transport, import, culture, language, infrastructure, supply chain, legal and safety matters
- Unpredictable changes in local conditions at the destination are usual, but jeopardize the complex interaction of all planning steps.
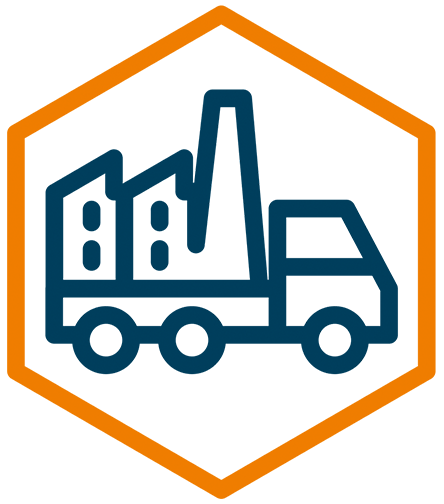
Are you looking for a competent partner with the appropriate experience and network?
Concerning the particular initial situation, we can offer you the following services.
Service profile production relocation
We offer:
- planning support based on realistic feasibility studies—integration of proven fall-back solutions for each project phase.
- establishing a local agent network for customs, infrastructure and jurisdiction. Supply chain installation, site analysis and development.
- coaching for interface management with a rapid change of perspective and independent management reporting. Cultural and language support.
- coordination of the implementation and, if necessary, project management on site.
- deployment of Augmented Reality* to generate content as well as for contactless and efficient implementation for the specialists during the on-site installation.
Our services are carefully coordinated with the customer and are tailored to the practical requirements. We also offer integrated solutions in the form of turnkey relocations.
*With the use of AR technology, presentations of complicated facts, as well as assembly steps, are generated simply. On-site, they are worked through interactively with the control center. AR reduces on-site personnel deployment.
The relocation of production abroad
After production relocation abroad “boomed” at the beginning of the millennium, the trend has reversed several times since then. The crises in the financial sector and the corresponding crumbling of sales led to a new thinking in the years around 2009. After that, the topics of back-reshoring or near-reshoring dominated the scene for a time. However, the shift back to a German location or at least to a location in the nearer (Eastern) European country was not only a reflection of purely economic reasons.
Often enough, companies had to draw the consequences of inadequate risk management – as well as pay a considerable lesson for unsolvable problems on site. Pure process thinking is simply not enough to overcome the many challenges of intercultural understanding and the great differences in work ethics and management culture.
The global trend toward relocating production is still alive
In the last 10 years, however, the direction of the number of production relocations has again been pointing steeply upward. In the metal and electrical industries in particular, the relocation of production to a site abroad has increased by around 80% since then, at least among large companies with several thousand employees. It is expected that the share of production abroad will soon be up to 40%. The pandemic, like political developments, however, is revealing new limits.
The temporary closure of major ports in China, the growing in-house demand for semiconductors, the Brexit – these are massive changes in processes in a very short time. They are causing global supply chains to stall for many companies and in some places causing production in Germany to collapse. The delays and the cost increases are also affecting suppliers in other Asian countries, who can no longer meet their obligations without restrictions.
What are the pros and cons of relocating production?
Accordingly, fears are being voiced loudly that the ongoing relocation of production by companies away from Germany should be stopped in order to reduce the dependency of industry. But even these reports are actually more like headlines for the business magazines. The relocation of production, with some “dents” in its development, remains an essential and important project for larger companies. This is shown by practically every serious survey conducted in the recent past. However, one aspect of it deserves far more attention than before.
The complexity of production relocations is much greater and more extensive than the easily calculated figures of many management consultants would suggest. The analysis of the respective starting position of the companies, the detailed consideration of all possible risks, the economic and cultural situation in the target country and literally thousands of other factors want to be thoroughly looked at.
Thorough analysis is the main ingredient of successful consulting
This is where the expertise of Faircom Industries comes into play. Unlike some consulting firms, the experts at Faircom and its international network are experienced practitioners for whom national and international production relocation means much more than playing with big numbers. Certainly, in an initial analysis, we can provide an assessment of the possibilities, risks and opportunities, on the basis of which the company management can decide whether more money should be spent at all on planning a production relocation.
Such a preliminary assessment by an independent party can weigh more heavily than many a favorable forecast by up-and-coming careerists in one’s own company. At Faircom Industries, we clearly prefer to close a project that seems too risky at this point than to put your production relocation and our reputation at risk in the long run. But if the green light can be given after the initial assessment, we’ll make sure that every single phase is worthwhile for you as the client
General conditions of the production relocation
Before signing a contract, we would prefer that the client has already intensively dealt with the market and product development for its offer when awarding the contract to us. Technological progress, possible changes in consumer behavior and also the behavior and strategies of competitors – all these factors should already have given the green light for the conditions of a production relocation.
The mere reduction in costs due to currently still lower wages in the target country is rarely sufficient as a justification and drive for such an undertaking today. But we assume that you have included even more weighty reasons in your planning.
This could also be interesting for you: